Clean in Place Systems
Over the years we have designed and built many CIP systems including simple single use systems, to full recovery systems and also more complex CIP strategies to cover full site wide recoveries, clean-up and re-use.
Activities are split between membrane and non-membrane engineering.
Contact us to discuss your particular application
Re-Use Systems
The most commonly requested CIP system these days is what is known as Re-Use CIP or Recovery CIP systems. These can vary from a fairly basic recovery of one main chemical, right through to a recovery of all chemical solutions and also the flush waters. With proper design and tuning these systems can result in remarkable savings in chemical usage, water usage, effluent volumes, effluent pH adjustment and effluent salt volumes.
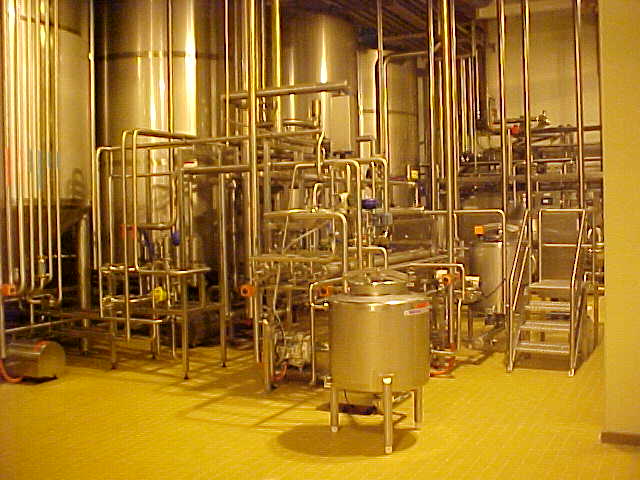
Caustic Recovery, Acid Recovery
In recent years EPI has installed several very successful chemical recovery and chemical re-use systems, both in new plants and retrofitting existing operations. Obvious benefits are chemical savings, effluent TDS reduction and effluent pH control. Depending on the application 80-90% of the chemical solution can be recovered for re-use. This applies to both the caustic and acid streams. By applying this percentage to your own chemical and effluent figures, you will get an idea of the savings to be had. Customised solutions can include clarification and NF or UF membrane treatment. Ideal applications are “use and dump” systems, such as evaporator CIP.
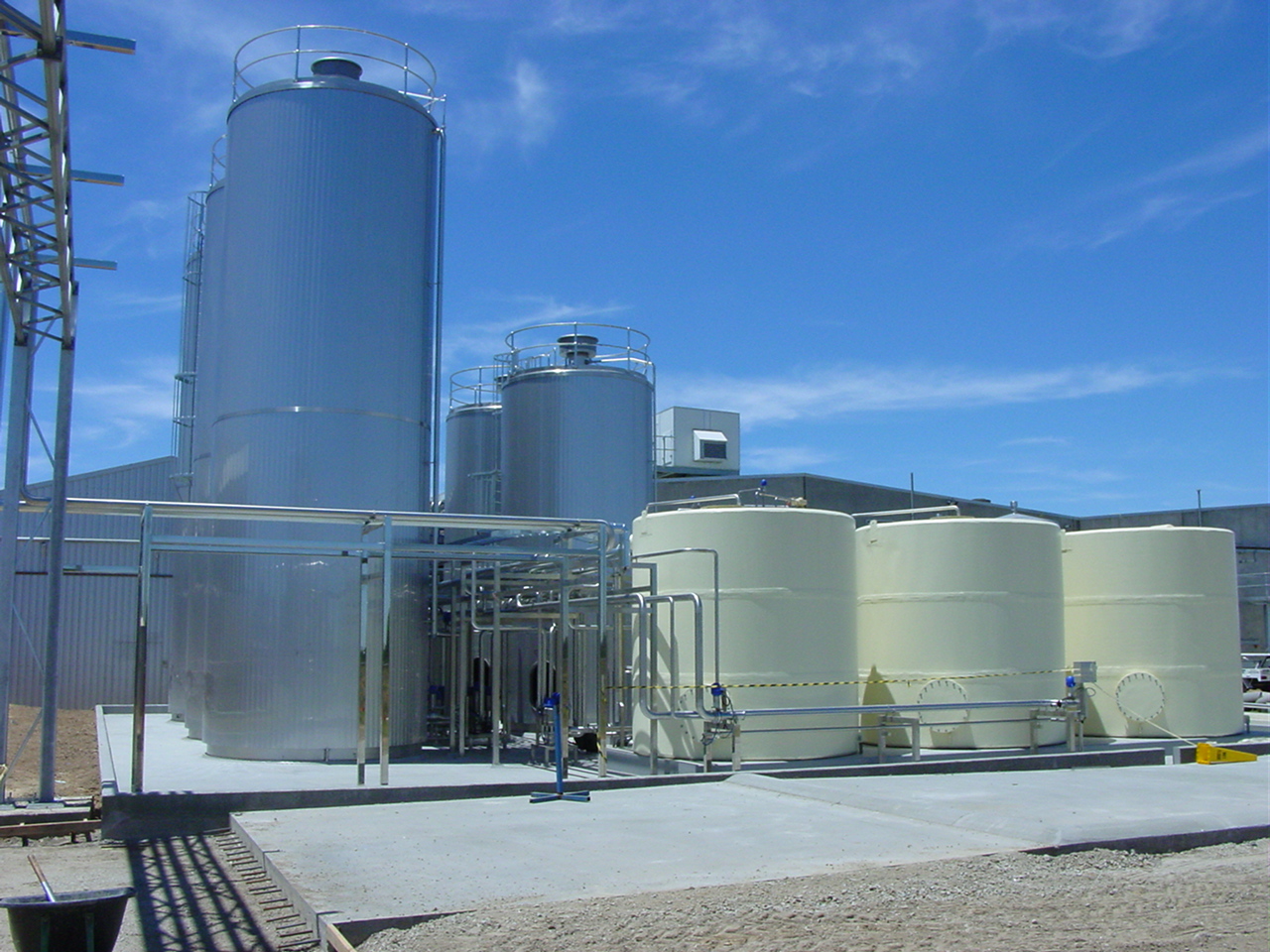
Site Wide Strategies
Where sites are more complex and with many different operating areas, it is important to consider the optimal solution for the total site. There is often the chance to centralise CIP recovery systems to reduce capital costs, reduce health and safety compliance costs and improve CIP recoveries. This is particularly so if an advanced chemical clean-up system (as above) is being considered. As always, every site has its quirks.
Single Use Systems
There is still an occasional place for single use or “use and dump” CIP systems. These are usually much lower capital cost but higher running cost. Single use is applicable where there is a very low number of cleans, or it is vital that there is no risk of product contamination from dirty re-used chemical, or the chemical will become extremely dirty during the wash and hence be unsuitable for re-use.
CIP Engineering Services
We have the in-house capability to assist with improvements to existing CIP systems. The majority of existing systems are not running to their full potential, usually due to tuning or engineering issues. The most common services we get involved with are:
- Plant audits – a CIP system review covering engineering design, equipment issues, plant optimisation, maintenance issues, operating procedures, system performance.
- Capacity upgrades of existing plants. This is most commonly the addition of another parallel set of circuits to handle a growing number of cleaning circuits.
- Automation of plants – older plants can be made more reliable, more energy efficient and less polluting by retrofitting automatic control.
- Tuning – Often plants are reasonably well designed from an engineering point of view, but have either been hastily commissioned or applications have changed so that the systems are very inefficient in chemical, energy and water usage. Tuning and operator training can make a huge difference for a modest outlay.